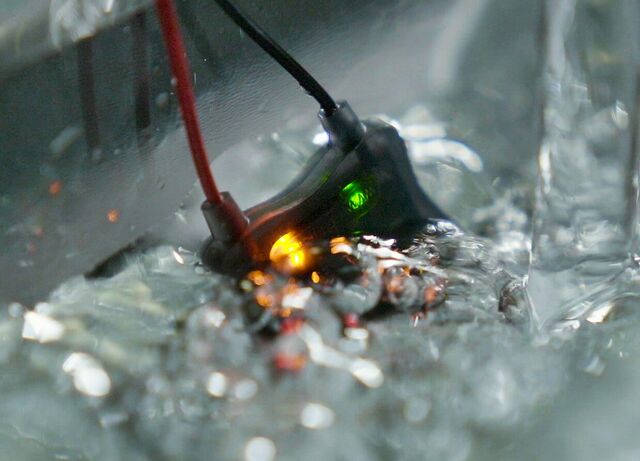
The Low Pressure Moulding process has its origin in the sealing of cable harnesses in the automotive industry - today it is used in many areas for the protection of electrical and electronic components.
At 5 - 60 bar, processing takes place at a significantly lower pressure than in the classic Injection moulding process. This makes it possible to directly encase sensitive components such as circuit boards, sensors, etc.
The cycle times are limited to the moulding cycle, which, depending on the size and contour of the components, is around 10-60 seconds. Direct further processing is then possible, which means a clear time advantage compared to e.g. 2-component potting.
The adhesive properties of the materials used enable the components to be protected up to IP68 with the right combination of materials.
Thanks to an optimised material flow, hotmelt molding with the thermoplastics used can also be implemented for temperature-sensitive components.
Different material properties and processing variants, combinations of different materials and, if necessary, further process steps enable a wide range of applications.
White Paper & Solutions Guide
Get detailed, exclusive insights into the technique of Low Pressure Moulding.
In addition to how it works and possible applications, our White Paper conveys the technological basics and provides insights into the emergence and development of the technology.
The Solutions Guide acts as a reliable guide so that you can implement your project efficiently and precisely with Low Pressure Moulding technology.
You will gain in-depth and experience-based insights into the world of electronic moulding with Low Pressure Moulding.
If you would like to receive the White Paper or the Solutions Guide as a free PDF, please use the contact form and you will receive the file by e-mail shortly.
Until you receive the complete file, you already have access to an extract of the White Paper.
LPM in a nutshell
- Low pressures
- Short cycle times
- No curing or reaction times
- Housings can be replaced
- Suitable as strain relief
- Applicable for temperature-sensitive components
- Operating temperatures -50°C - + 150°C
- Impermeability up to IP68
- Wide range of applications
We would be happy to organise technology trainings for you and your colleagues to get to know the possibilities and evaluate the use cases in your company - on site or online from the OptiMel Studio.
Fields of application
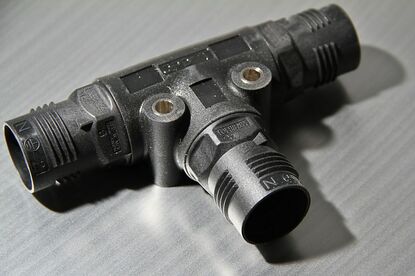
Connectors / Grommets
Housing and sealing with integrated strain relief and kink protection can be implemented for plug connections and grommets. A defined position of the components and, if necessary, plugging is implemented in the tool by means of a specially manufactured moulding cavities, clamping plates and mating connectors.
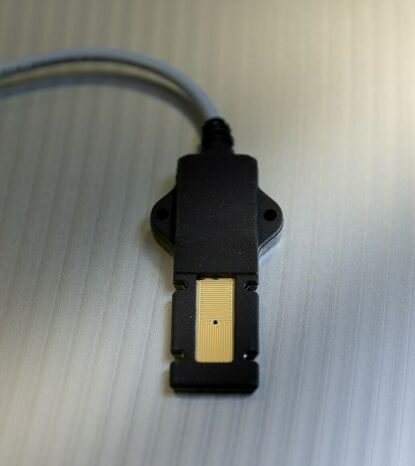
Sensors
Sensors are protected from a multitude of external influences without affecting their functionality. They can be completely encased or, by using the adhesive properties of the materials, important measuring areas can be kept free from encapsulation and at the same time important electronics areas can be protected against media. In both cases, component damage is avoided thanks to the low pressures of the LPM process.

Housings
Individual shaping and sealing in one process step, which results in - additionally to the technical advantages made possible by the sealing - in particular the possibility of higher production quantities per time unit and thus significant cost savings.
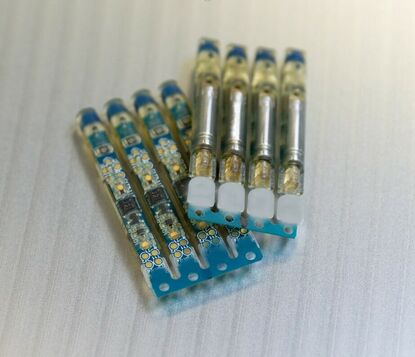
PCBs
The encapsulation serves to protect the components from vibration, moisture, contamination, contact and mechanical stress without influencing or damaging them within the processing.
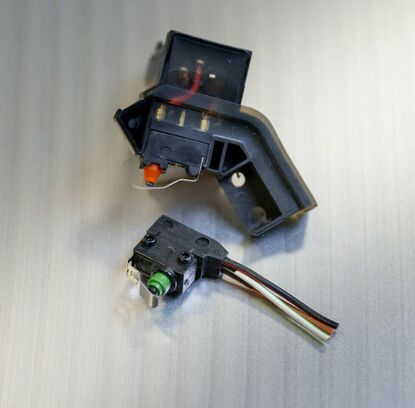
Micro switches
Low Pressure Moulding is in this case mainly used to ensure long-term functionality, by protecting against humidity.
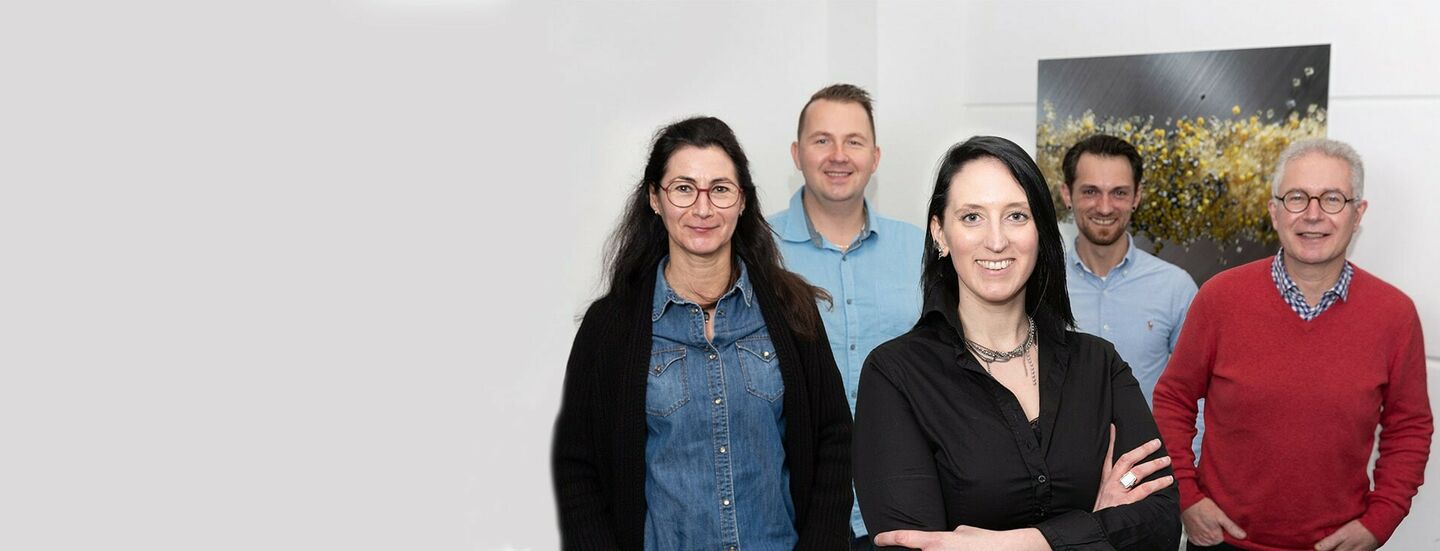
Would you like to find out more details about the technology? Do you have any projects that you would like to discuss with us?
We are looking forward to hearign from you!