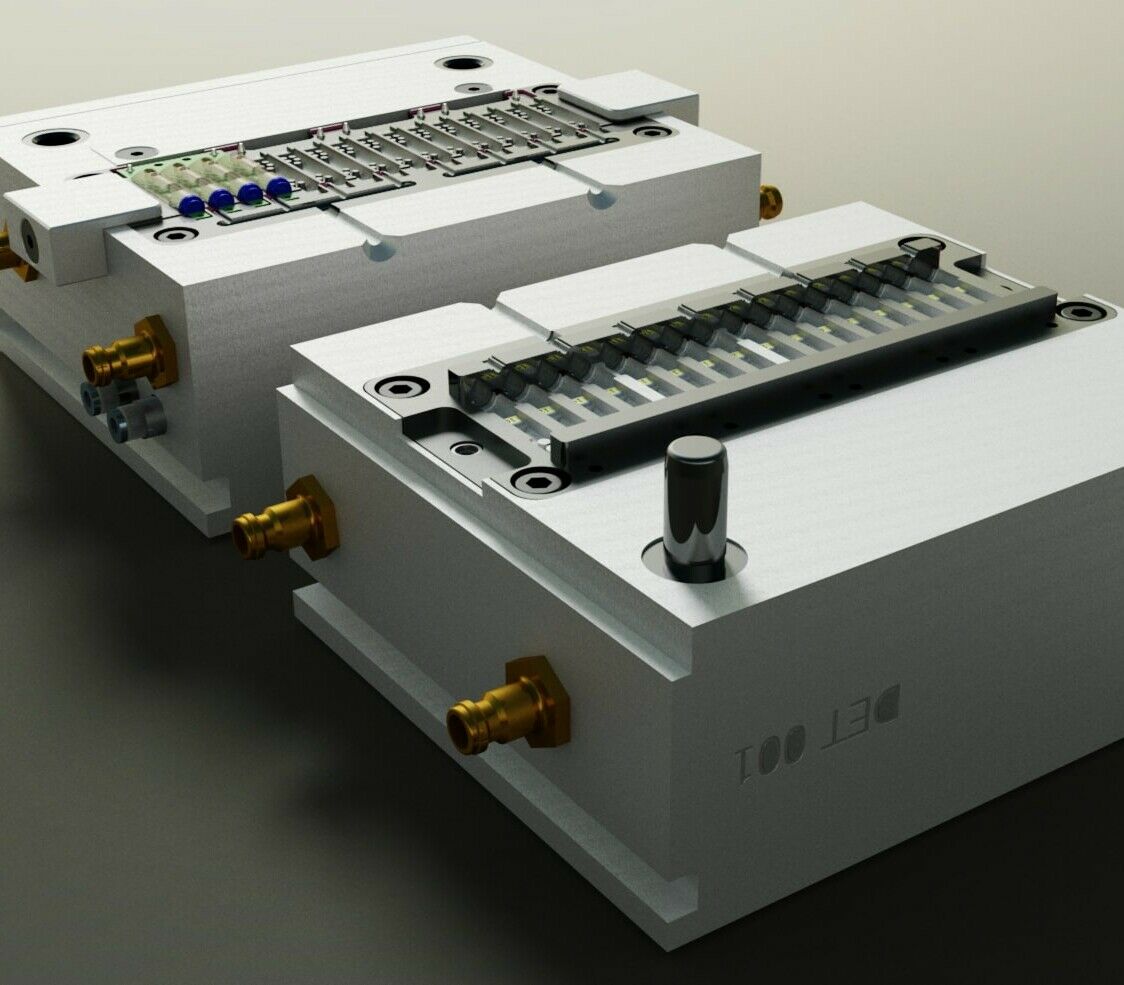
The decisive factor for the technical implementation of any project is the appropriate moulding tool. Each one is developed, designed and manufactured individually for the respective project. The design of the tools results from the combination of customer requirements as well as material and process-related principles. Individual design features are comparable to those of the classic injection moulding technology. A significant difference results from the properties of the moulding materials used. The low-viscosity thermoplastic hotmelts are processed with low pressures and have adhesive properties - two essential points that must be taken into account when designing the tool. Due to a large number of already implemented projects for hotmelt tools, our designers and project managers have extensive experience in this area. Use it for your project and contact us. We gladly support you and are at your disposal to any extent, from advice to design and complete production.
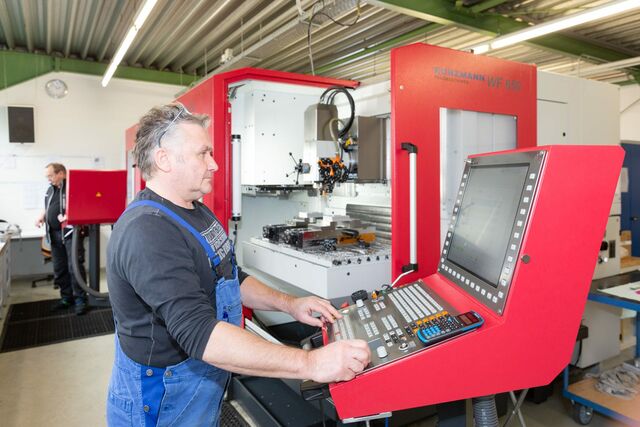
Own tool shop
In order to achieve optimised and reliable results in sophisticated projects, every detail counts. The moulding tools represent a decisive factor and are a game changing parameter. In combination with a precisely aligned process, high-quality results are achieved.
In addition to the design of a tool, production plays a decisive role. Principles from other manufacturing areas can only be transferred to the requirements of the Low Pressure Moulding to a certain extent and knowledge of the technology is of important influence.
So it is consistent for us to have this core competence as a moulding tool manufacturer in-house. Our employees have many years of experience in the field of Low Pressure Moulding and know the influence of every single detail on the process.
Moreover during mould trials in our technical center or on the respective customer system, the production parameters are determined and optimised with regard to the respective project requirements.
Flexibility in production and quick reactions to reworking as well as necessary adjustments and repairs top off the advantages.
Process optimisation by means of tool design
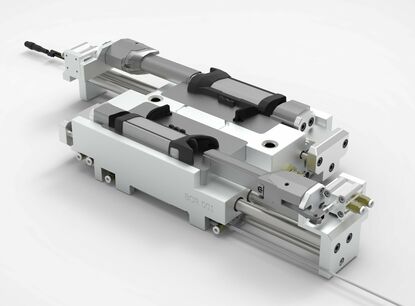
Component fixture
For positioning, avoiding air inclusions, optimised demoulding and component geometry.
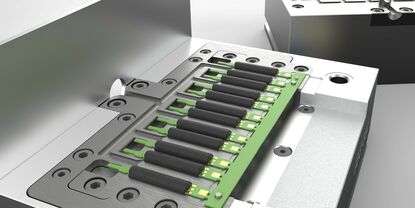
Specific sprue direction
To multiply the cavities while shortening the flow path and reducing waste volume or optimising temperature control.
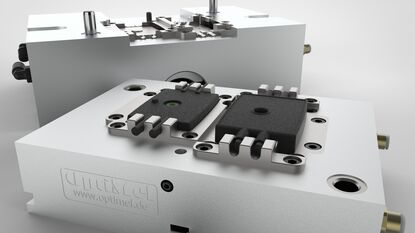
2-step processes
Two cavities for pre- and main moulding for centering components, avoiding air inclusions and combining material properties.
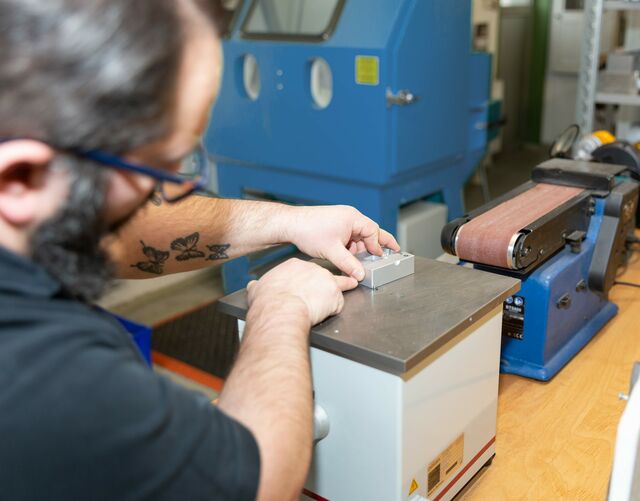
Prototype construction and sample production
The creation of samples and prototypes is an important factor for the implementation of a project. Feasibility studies and tests can be carried out on the basis of prototypes. Using sample tools close to series production, the construction data are checked for successful implementation and adjusted if necessary, and the basic process parameters for subsequent series production are determined.
Be there live when sampling without the effort of a trip?! - We'll switch you into our studio and it's almost like you're there.
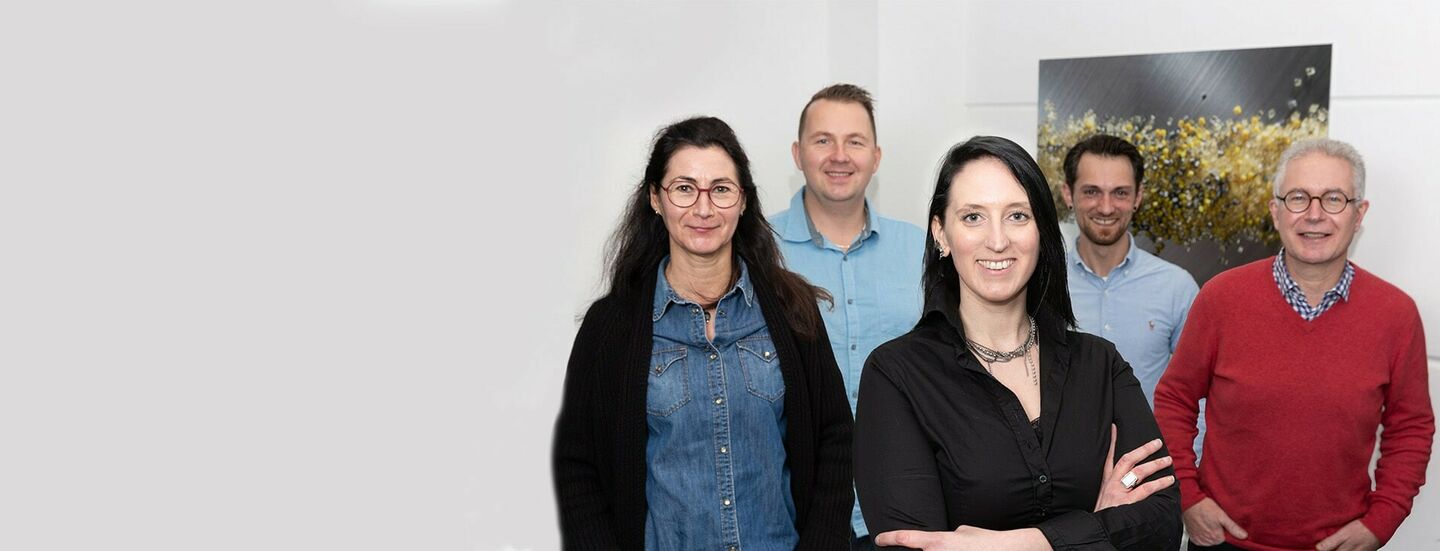
Do you need advice on moulding tools for your projects or an individual offer?
Contact us!