Your partner for machines and production materials
Based on years of experience and with the aim of maximum flexibility, we have developed a machine system that is oriented towards the respective requirements.
We no longer built any standard models - our modular system including machines and accessories can be precisely tailored to your projects and production conditions.
Please, find the suitable equipment for your project here,
We deliver all available Technomelt® materials for the Low Pressure Moulding technology - with flexible and service-oriented offers for your respective project.
Samples are just as possible here as individual delivery quantities and delivery schedules, through to annual framecontracts with corresponding special conditions.
Find the right material here,
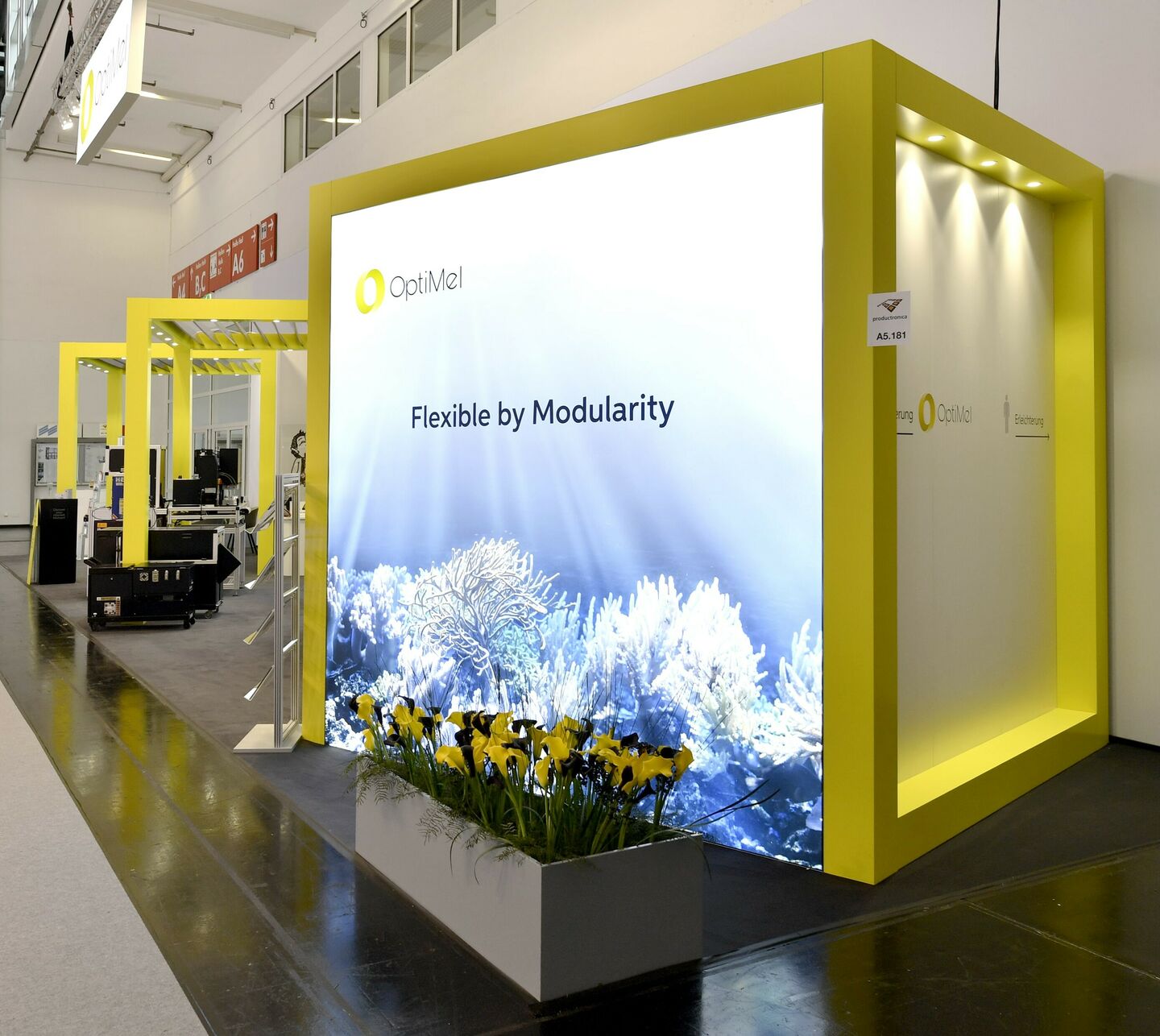
What pioneers consider important
For us, it is not only important what we do - full service in Low Pressure Moulding - and why we do it - in order to offer our customers an optimal solution for the protection of electrical and electronic components - but also how we do it - with awareness and responsibility for our environment and ourselves. We are convinced that everyone contributes to what kind of world we will live in in the future. That is why we want to live up to our responsibility as a company in the industrial state of North Rhine-Westphalia and, with our commitment and our decisions, contribute to sustainable business that is oriented towards the common good.
Picture: Wiesner Messearchitektur GmbH